Tungsten Metal Powder
Tungsten Metal Powder Vibrating Screen solutions
Metal tungsten powder is an important industrial raw material, widely used in cemented carbide, electronic materials, special steel and nuclear industry. The particle size of tungsten powder directly affects the performance and application effect of the product. Therefore, the screening process is very important in the production process of metal tungsten powder.

Metal tungsten powder preparation process
The production process of metal tungsten powder mainly includes several key steps such as raw material preparation, reduction reaction, screening and packaging.
- Raw material preparation: Use tungsten trioxide (WO₃) or ammonium paratungstate (APT) as raw materials, and ensure the purity and particle size meet the standards after screening and pretreatment (such as ammonium paratungstate needs to be calcined into tungsten trioxide).
- Reduction reaction: In a tubular electric furnace or a rotary furnace, tungsten trioxide is reduced to tungsten dioxide at 500-700℃ by hydrogen reduction method, and then further reduced to metal tungsten powder at 700-900℃. The process needs to strictly control the hydrogen flow, temperature and time to ensure the quality of tungsten powder.
- Screening and packaging: Use professional screening equipment to grade the particle size of tungsten powder, and use polyethylene plastic bottles or iron barrels and other materials to seal and package to prevent moisture, oxidation, etc.
- Quality control: Monitor the purity, particle size and other key indicators of raw materials, intermediate products and final products throughout the process. During this process, need to use a test sieve shaker to analyze particle size, to ensure that the quality of metal tungsten powder meets the application requirements.
Tungsten powder characteristic analysis
The quality of tungsten powder directly determines the quality of tungsten carbide and the performance of alloys. The classification of tungsten powder can effectively modify the powder’s properties, solving issues related to coarse and fine powder mixing, and reducing the discrepancy between fine, coarse, and average particle sizes. This process allows for the production of coarser and more uniform tungsten carbide powder. Due to the characteristics of tungsten, which makes it difficult to crush, appropriate pre-classification and crushing can help break up agglomerated particles, leading to better powder separation and improved uniformity.
Metal tungsten powder screening requirements
- Purpose: Fine grading of tungsten powder
- Screening mesh: 60 mesh to 325 mesh
- Requirements: Tungsten powder has strict requirements on impurity content and oxygen content. During the screening process, measures must be taken to prevent the tungsten powder from reacting with oxygen in the air, increasing oxygen content. Sealed screening equipment must be used.

Recommended equipment solution
Ultrasonic Vibrating Sieve
- Material: metal tungsten powder
- Equipment: ultrasonic rotary vibrating sieve
- Output: 100kg-3 ton/h
- Screening particle size: 30-60 mesh, 60-100 mesh, 100-150 mesh
- Application: Ultrafine powder (tungsten carbide powder, silicon carbide powder, alloy tungsten powder, tin powder, etc.)
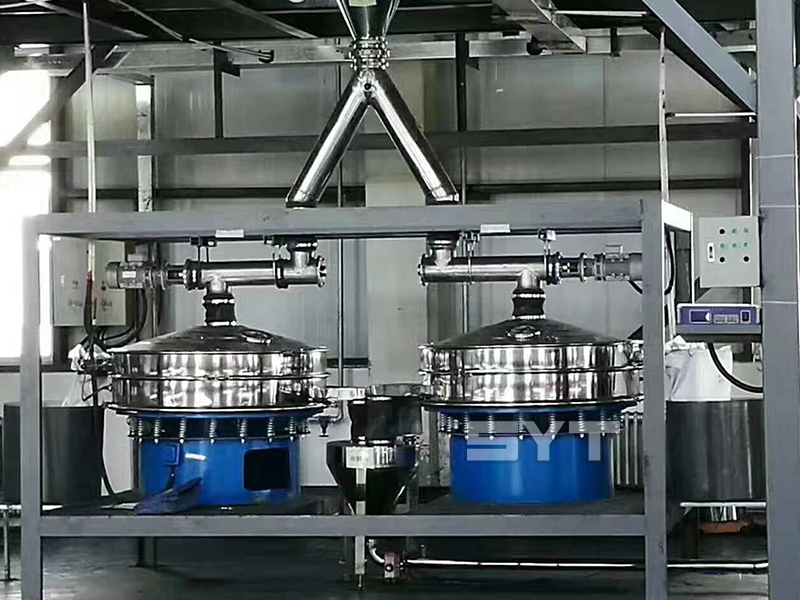
Features of tungsten powder vibrating screen
- Ultrasonic anti-blocking technology: Equipped with an ultrasonic system, the screen mesh is not easy to block, the screening process is smooth, and the screening efficiency is improved.
- Low noise: The equipment has low operating noise.
- Efficient processing of difficult-to-screen materials: Solve the screening problems of strong adsorption, high density and easy agglomeration of ultrafine powder materials.