Dewatering vibrating screen is a vibrating screening equipment used for material dehydration and solid-liquid separation. It mainly removes moisture from materials through the combination of high-frequency vibration and screen mesh,It is widely used in mining, chemical, food, environmental protection, coal and other industries. In the field of industrial screening, especially in the industrial activities of sand making and sand screening, dewatering screen is the key equipment. Xinxiang Sanyuantang Machinery Co., Ltd. relies on more than 30 years of technical accumulation and innovation strength, and is committed to providing customers with efficient, stable and energy-saving dewatering screen equipment to help enterprises achieve a double increase in production efficiency and economic benefits.
- Number of screen layers: single or multi-layer
- Screen hole size: 0.1mm~50mm
- Screen surface inclination: 10°~25°
- Vibration frequency: 700~3000 times/minute
- Amplitude: 2~10mm
- Processing capacity: 5~200t/h
- Moisture content after dehydration: 10%~25%
Working principle
Dewatering vibrating screen realizes solid-liquid separation through high-frequency mechanical vibration and screen mesh filtration. The materials are evenly distributed on the inclined screen surface, the vibration makes the particles loose, the liquid is discharged through the screen, and the solid is retained because the particle size is larger than the screen hole; the multi-layer screen mesh can be equipped with optional grading dewatering, and the final dry solids are discharged by vibration conveying.
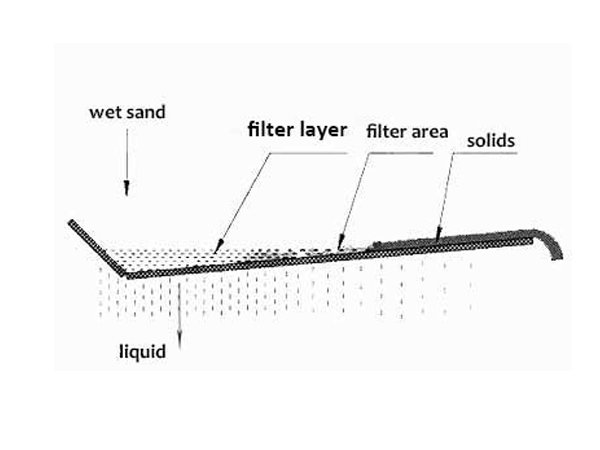
Dewatering vibrating screen structure
The dewatering vibrating screen is a high-efficiency solid-liquid separation equipment. Its structural design fully considers the requirements of mechanical strength, vibration characteristics and process. The whole machine is mainly composed of the following core parts:
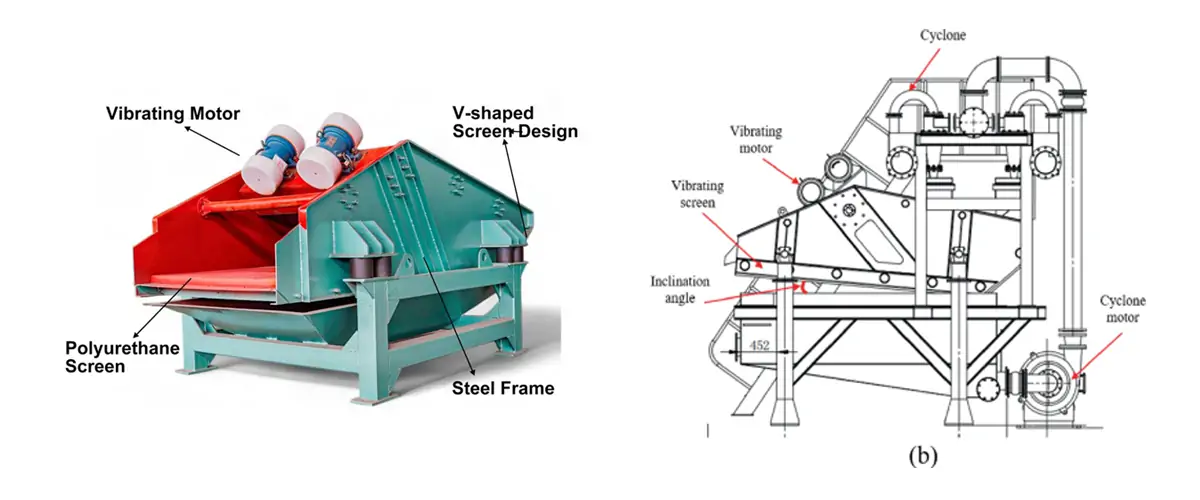
- Main frame structure:The box beam welding structure is adopted, and the main material is low-alloy high-strength steel. The lateral reinforcement structure is set inside the screen box to effectively control the deformation of the box during long-term work.
- Working screen surface system:It is equipped with multi-layer modular screen plates, and the standard polyurethane elastomer screen is adopted, which has excellent wear resistance and anti-blocking performance. The inclination angle of the screen surface can be adjusted in the range of 10°-25° through the hydraulic adjustment device to adapt to the dehydration characteristics of different materials. The screen tension adopts a hydraulic automatic compensation system to ensure constant tension during work.
- Vibration generating device:A dual-motor self-synchronous vibrator is adopted. The directional exciting force is generated by the precisely counterweighted eccentric block, and the vibration frequency can be adjusted in the range of 700-1500rpm. The vibrator shell is made of cast iron material, and a lubricating oil circulation system is set inside to ensure long-term stable operation.
- Elastic support system:Multi-layer composite rubber springs are selected as the main shock-absorbing element.
- Transmission and control system:Equipped with variable frequency speed regulating motor, power transmission is achieved through universal coupling. The control system integrates vibration monitoring, temperature protection and overload alarm functions, which can realize remote monitoring and intelligent adjustment.
Details Show
Dehydration Vibrating Screen Specifications
Category | Parameter | Range/Options | Notes |
Basic Parameters | Screen Size | Width: 500-3000mm | Common sizes: 1000×2000mm, 1500×4000mm, etc. |
Length: 1500-6000mm | |||
Processing Capacity | 5-300 t/h (Custom up to 500 t/h) | Depends on material characteristics | |
Motor Power | 1.5-110 kW | Sized for load requirements | |
Technical Specs | Vibration Frequency | 700-1500 RPM | Adjustable with VFD |
Amplitude | 2-8 mm (Adjustable) | Modified via eccentric weights | |
Screening Efficiency | 85%-95% | Lower for fine particles | |
Discharge Moisture | Standard: 8%-25% | Varies with feed moisture | |
High-Efficiency: 5%-8% | |||
Structural Config | Screen Decks | 1-4 layers | Multi-layer for classification |
Screen Material | Stainless Steel/Polyurethane/Rubber | Polyurethane offers best wear resistance | |
Aperture Size | 0.1-50 mm | Selected based on separation needs | |
Inclination Angle | Fixed: 15°/20°/25° | Hydraulic or mechanical adjustment | |
Adjustable: 10°-25° | |||
Special Models | Explosion-Proof | Complies with ATEX/GB Standards | Equipped with Ex-rated motors & controls |
Corrosion-Resistant | 316L Stainless Steel/Special Coatings | For chemical/marine environments | |
High-Temperature | Operating Range: -30°C to 150°C | Special seals & lubrication |
Features
The technical characteristics of the dewatering vibrating screen are mainly reflected in three aspects: high efficiency, adaptability and reliability. The equipment realizes the refined dehydration of various materials through optimized mechanical dynamics design and advanced separation technology.
- Efficient dehydration: Efficient high-frequency vibration (700-1500 RPM) and multi-layer screens quickly reduce moisture content to 5%-25%, with a processing capacity of 5-500 tons/hour.
- Precise vibration control: The amplitude (2-8 mm) and frequency can be precisely adjusted to achieve the best dehydration effect for different materials
- Anti-clogging technology: The elastic screen with secondary vibration and optional high-pressure spray/ultrasonic system prevents fine particles from clogging and ensures continuous operation.
- High-quality materials: Made of carbon steel, stainless steel (304/316L) or special alloys, with high temperature resistance (-30°C to 150°C) and optional explosion-proof/dust-proof/corrosion-proof design.
- Intelligent monitoring: Integrated sensors provide real-time vibration adjustment, fault alarms and adaptive performance optimization for various materials.
- Convenient maintenance: The quick-change mechanism of the screen can complete the replacement operation within 30 minutes, and key components are equipped with convenient maintenance ports.
Cases Show
application scenarios of dewatering vibrating screens
Industry Sector | Typical Materials | Processing Requirements | Key Equipment Configurations | Process Outcomes | Technical Advantages |
Mining | 1. Iron/copper tailings 2. Concentrate dewatering 3. Mineral processing wastewater | 1. Capacity: 200-500 t/h 2. Moisture content ≤18% 3. High wear resistance required | 1. Multi-layer heavy-duty screens (3-4 layers) 2. High-chromium alloy screen panels 3. Dual-motor self-synchronized vibration system | 1. Tailings moisture: 15-18% 2. Water recovery rate ≥90% | 1. High throughput capacity 2. Screen life ≥8000 hours 3. Handles high-density slurries (40-60% solids) |
Coal | 1. Coal slime 2. Clean coal dewatering 3. Gangue recovery | 1. Particle size: 0.5-10 mm 2. Capacity: 100-300 t/h 3. Explosion-proof requirements | 1. Polyurethane anti-blinding screens 2. Explosion-proof motors (ExdⅡBT4) 3. Adjustable inclination (15-25°) | 1. Coal slime moisture: 20-25% 2. Clean coal moisture ≤8% | 1. Energy savings >30% 2. Explosion-proof safety design 3. Handles high-ash materials (ash content ≥20%) |
Environmental | 1. Municipal sludge 2. Industrial sludge (textile/paper) 3. River dredging | 1. High viscosity (500-2000mPa·s) 2. Solids content: 3-10% 3. Odor control | 1. 316L stainless steel screens 2. High-pressure spray system 3. Fully enclosed structure with deodorization ports | 1. Dewatered solids ≥25% 2. Capacity: 20-100 t/h | 1. Corrosion-resistant construction 2. Anti-clogging design 3. Compatible with flocculant dosing systems |
Chemical | 1. Fertilizer crystals 2. Salt dewatering 3. Polymer granules | 1. Corrosive media (pH2-12) 2. Product purity ≥99% 3. Fine particles (0.1-1mm) | 1. Titanium/PP screen materials 2. Variable frequency drive (0-1500rpm) 3. Gas protection system | 1. Crystal moisture ≤5% 2. Fine particle loss ≤3% | 1. Acid/alkali resistant 2. Product contamination-free 3. Precise classification (±0.05mm) |
Building Materials | 1. Manufactured sand 2. Quartz sand washing 3. Aggregate classification | 1. Capacity: 50-200 t/h 2. Clay content ≤1% 3. Gradation requirements | 1. Double-layer screens (3mm/0.5mm) 2. Wear-resistant rubber lining 3. Water recycling system | 1. Sand moisture ≤7% 2. Fines content ≤5% | 1. Wear parts life ≥6000h 2. Simultaneous washing+dewatering 3. Adjustable product gradation |
Metallurgy | 1. Steel slag 2. Bauxite dewatering 3. Precious metal recovery | 1. High-temp materials (≤150°C) 2. Hard particles (Mohs ≥7) 3. Metal recovery ≥95% | 1. Heat-resistant steel screens 2. Air cooling system 3. Metal detection/sorting | 1. Slag moisture ≤10% 2. Metal recovery: 97-99% | 1. High-temperature design 2. Metal wear protection 3. Integrated metal sorting options |
Food | 1. Starch dewatering 2. Fruit/vegetable pomace 3. Yeast separation | 1. Food-grade standards (FDA) 2. Low-temp processing (≤40°C) 3. Non-contamination | 1. Polished 304 stainless steel 2. CIP cleaning system 3. Food-grade lubrication | 1. Starch moisture ≤12% 2. Protein retention ≥90% | 1. GMP compliant 2. Hygienic design 3. Nutrient preservation |
(Note: The data in the table is based on standard models. For special needs, detailed technical agreements need to be communicated with engineers)