
The metal powder screening and conveying system is a high-efficiency processing equipment designed for fine, easily airborne metal powders such as ferroalloy powder and hard alloy powder. This system enables full automation and dust-free handling from raw material feeding to finished product packaging, ensuring a clean production environment and stable product quality.
- Material Processed: Metal Powder
- Capacity: 100-2000 kg/hour
- Screening Mesh Size: 80 mesh – 500 mesh
- Equipment Configuration: Rotary vibrating screen, vacuum feeder
System Components:
Material cart/drum → Vacuum conveying → Buffer → Screening → Packaging.

System Description:
Raw Material Feeding:
Raw materials are fed directly into the system via a material cart or drum, reducing manual intervention and improving operational safety.
Vacuum Conveying:
A vacuum feeder is used as the core conveying device, utilizing negative pressure to smoothly and continuously draw metal powder from the storage unit and transport it to the next stage through sealed pipelines. This process effectively prevents powder from becoming airborne, maintaining a clean production environment.
Buffer Stage:
The powder is temporarily stored in a buffer tank, which balances fluctuations in flow between the upstream conveying and downstream screening, ensuring stability during the screening process. The buffer tank is designed with anti-stick and anti-blocking structures to prevent powder buildup and clumping.
Precision Screening:
The rotary vibrating screen, as the core of the screening process, features a unique vibration mechanism and high-efficiency mesh design, allowing precise screening within the 80 to 500 mesh range. The screen can be quickly replaced to accommodate the production of products with different particle size requirements. The vibration intensity is adjustable, ensuring both screening efficiency and the prevention of excessive powder breakage.
Packaging Stage:
After screening, the metal powder is directly fed into automatic packaging equipment for quantitative packaging, reducing manual contact and improving packaging efficiency and hygiene standards.
Recommended Equipment
Application Materials
The metal powder screening and conveying system is mainly used for handling various metal powders and related materials.
- Iron-based powders: Including pure iron powder, stainless steel powder, alloy steel powder, etc.
- Non-ferrous metal powders: Such as aluminum powder, copper powder, nickel powder, titanium powder, etc.
- Hard alloy powders: Powders made from high-hardness carbides (e.g., tungsten carbide, titanium carbide) mixed with metal binders (e.g., cobalt, nickel), as well as cermet powders.
- Magnetic powders: Such as ferrite powder, rare earth permanent magnet powder, etc.
- Composite metal powders: Powders composed of two or more metallic elements, manufactured through specific processes, with unique physical and chemical properties for high-performance materials.
- Metal oxide powders: Such as aluminum oxide powder and iron oxide powder, which, though not metal powders themselves, are used in certain processes (e.g., ceramic manufacturing, catalyst preparation) and require screening and conveying as raw materials.
System Features
- High Efficiency & Dust-Free: Full negative pressure conveying effectively prevents metal powder from becoming airborne, protecting the production environment and reducing occupational health risks.
- Precise Screening: The vibrating screen is well-designed with high screening accuracy, meeting various particle size distribution requirements and improving product quality.
- High Automation: From feeding to packaging, the entire process is automated, reducing manual intervention and increasing production efficiency.
- Flexible Configuration: Equipment configuration can be adjusted based on production needs, such as mesh size and conveying speed, to handle a variety of metal powders.
- Easy Maintenance: The equipment is reasonably designed for easy cleaning and maintenance, lowering maintenance costs and extending service life.
- Eco-Friendly & Energy Efficient: The system uses energy-saving motors and optimized air circuit designs to reduce energy consumption, aligning with green production requirements.
Metal powder screening and conveying system site
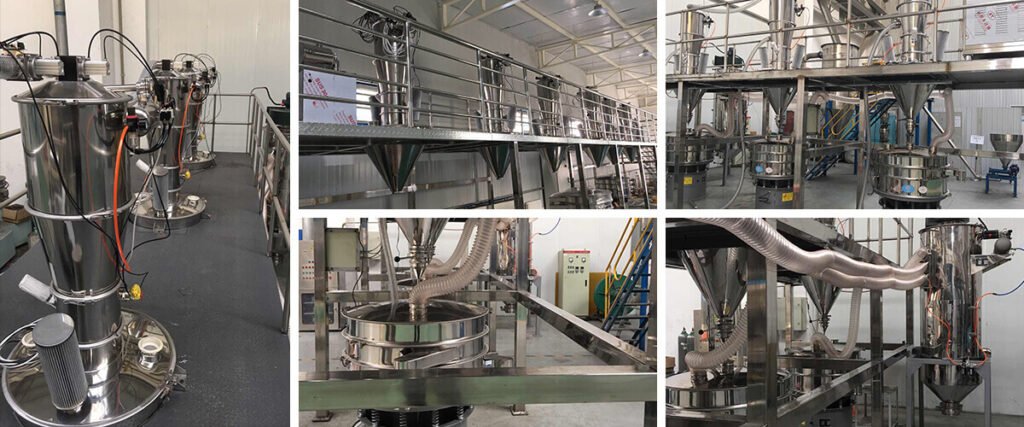