As a professional linear vibrating screen manufacturer, Sanyuantang is committed to providing customers with customized linear vibrating screen solutions. Linear vibrating screen is one of our company’s flagship products. We provide a variety of customization options to ensure that the production and process requirements of different industries are met. The following are several key aspects about customize linear vibrating screen:
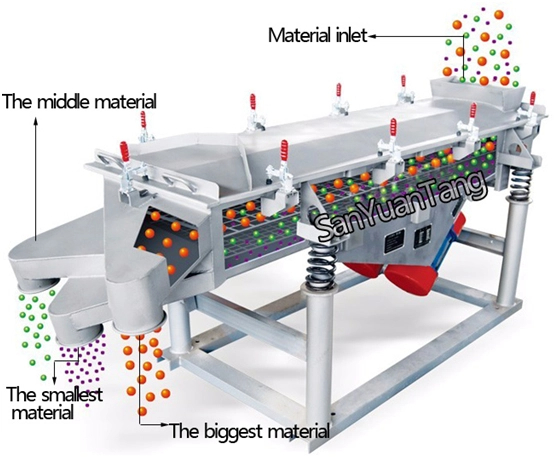
Table of Contents
Customized material
The material of the linear vibrating screen can be customized according to the specific needs of customers. Common material options include carbon steel, food-grade 304 stainless steel, 316L corrosion-resistant stainless steel, etc. Customers can choose the most suitable material according to the nature of the material, working environment and use requirements.
- Stainless Steel Linear Vibrating Screen
- Carbon Steel Linear Vibrating Screen
Customized size
The size of the linear vibrating screen, including length, width and height, can be tailored according to the customer’s production requirements and on-site space. The design of the size mainly takes into account production efficiency and coordination with on-site facilities, so that the equipment can operate efficiently.
- Large Linear Vibrating Screen Size
- Large Linear Vibrating Screen Size
- Mini Linear Vibrating Screen
- Mini Linear Vibrating Screen
Customized feed port
The size and shape of the feed port can also be customized according to customer requirements. Common feed port forms include rectangular, circular and flange interfaces. Customized feed ports can help the equipment better connect with upstream and downstream equipment and improve the overall efficiency of the production line.
- Square feeding port
- Circular feeding port
- Closed feed port
Customized discharge ports
The design of the discharge port usually depends on the characteristics of the screened material and the connection requirements with downstream equipment. Our company can provide different forms of customized discharge ports according to the material type, screening requirements and production process.
- Customized discharge ports
- Customized discharge ports
- Customized discharge ports
Customized sieves
We provide a variety of customized sieve options, including coarse wire screens, fine wire screens, steel plate cut hole screens and strip screens. Customers can choose the most suitable screen type according to the particle size and characteristics of the screened material to achieve the best screening effect.
- Metal Woven Mesh
- Grid
- Punching plate
Customized motor position
The motor position of the linear vibrating screen can be customized according to customer needs, and there are usually three options: top, bottom or side. The installation position of the motor is usually related to the height and installation environment of the equipment. Customers can choose the motor installation position according to the limitations of the on-site space.
- Downward vibration type
- Side vibration type
- Up vibration type
Select Linear Vibrating Screen Motors
Depending on the production environment and the nature of the material, customers can choose ordinary vibration motors or explosion-proof vibration motors. Explosion-proof motors are suitable for working environments with high dust concentrations, effectively preventing safety hazards such as dust explosions.
Special Customize Linear Vibrating Screen
Special customized linear vibrating screens are personalized designs for customers under specific working environments and production requirements. Compared with standard models, special customized linear vibrating screens can be customized according to actual conditions. For example, for places with special requirements such as dust prevention, cleaning or explosion-proof, we can provide customers with customized solutions with spray devices, dust removal systems or explosion-proof motors.
Customized spray device
For some materials that need to be cleaned or dusted, our company can customize a spray device for the linear vibrating screen. The device can lightly clean the material during the screening process to remove dust, while preventing the material from generating too much dust during the screening process.

dust removal device
In order to meet customers’ requirements for environmental hygiene, we can customize a dust removal system for the linear vibrating screen. The system includes a high-power exhaust fan installed above the equipment, and customers can adjust the position of the air duct according to the on-site conditions to achieve efficient dust removal.
- Linear Vibrating Screen with Dust Removal Device
- Linear Vibrating Screen with Dust Removal Device
add wheels
In order to facilitate the movement of the equipment, we designed movable wheels for the linear vibrating screen. The wheels are equipped with a locking device, which can ensure the stability of the equipment during work and can be easily unlocked when it needs to be moved, making it easy to move and adjust the position.

Customized color
We can also customize the color of the equipment according to the customer’s corporate image or other requirements to meet different aesthetic and brand needs.
- Blue
- Off-white
- Grey
Sanyuantang is a professional linear vibrating screen manufacturer in China. We have 30 years of production experience and provide a variety of linear vibrating screen customization options to meet the special needs of different customers. In addition, we can also provide customers with complete screening, conveying and crushing solutions to ensure the efficient and stable operation of various sand and gravel aggregate production lines.
Related Articles
- Use And Maintenance Of Linear Vibrating Screen
- Linear Vibrating Screen VS Circular Motion Vibrating Screen
- How To Choose Linear Vibrating Screen Motor?
- How To Choose Screen Mesh Frame Of Linear Vibrating Screen
- Differences Between Probability Screen And Linear Vibrating Screen
- Differences Between Linear Vibrating Screen And Rotary Vibrating Screen
- Linear Vibrating Screen For Ceramic Sand Sieving