In the mining, building materials, and metallurgical industries, crushers are key equipment for material crushing and processing. As the two most common crushing equipment, hammer crushers, and jaw crushers have their own unique working principles and application advantages. Understanding the difference between hammer crushers and jaw crushers is crucial for choosing the right equipment. This article will make a detailed comparison of the aspects of working principle, scope of application, advantages, and disadvantages to help you make the right equipment selection decision.
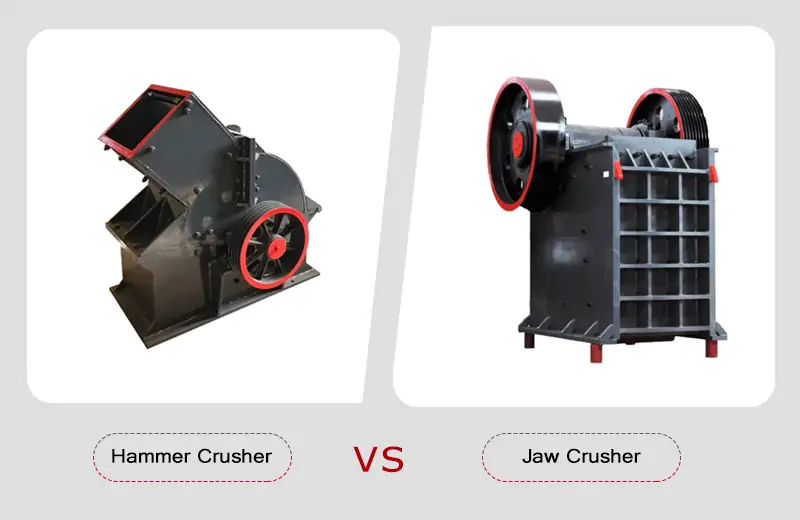
Table of Contents
Comparison Between Hammer Crushers and Jaw Crushers
Differences in working principles
The core components of the hammer crusher include the rotor, hammerhead, impact plate, screen plate, and transmission device. Its working principle is based on the fact that when the rotor rotates at high speed, the hammer head impacts, hits, shears and rubs the material multiple times. After the material enters the equipment, it is first hit by the hammer head and undergoes multiple collisions and crushing, and is gradually crushed to the required particle size. After this process, the crushed material is discharged from the equipment through the screen plate to complete the crushing task. The structural design of the hammer crusher ensures the efficient crushing performance of the equipment, especially for the processing of medium and soft materials.
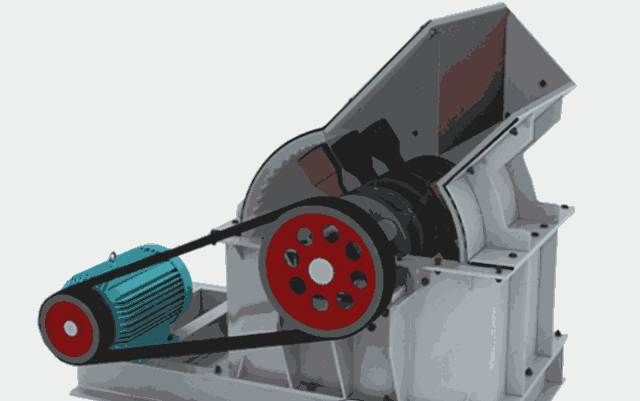
The jaw crusher is mainly composed of a frame, an eccentric shaft, a rotating part, a crushing chamber, a safety device, and a discharge port adjustment device. Its working principle is to crush the material by applying pressure to the material through the opening and closing movement of the upper and lower jaw plates. The upper and lower jaw plates are connected by an eccentric shaft and a connecting rod mechanism. As the eccentric shaft rotates, the upper and lower jaw plates are driven to move up and down. When the lower jaw moves upward, the material is clamped compressed, and crushed, and when the lower jaw moves downward, the crushed material is released. The material reaches the ideal particle size through multiple extrusions and compressions and is finally discharged through the discharge port. The jaw crusher has a simple structure, is easy to operate and maintain, and is suitable for processing materials with higher hardness.

Differences in applicable materials
The hammer crusher is suitable for crushing ore materials with relatively small particle size and hardness. It is usually used for medium and fine crushing of brittle and medium materials such as cement, coal preparation, coke, oil shale, chalk, gypsum, etc. Due to its impact crushing characteristics, the hammer crusher is particularly suitable for production occasions that require high output and finer material particle size. In the construction sand and gravel aggregate production line, hammer crusher equipment is rarely used as the primary crushing equipment.
- Coal Gangue
- Plaster
- Oil Shale
Jaw crusher equipment is mainly used to crush hard, medium-hard, and soft ores and other materials with high hardness, such as various ores, flux, slag, building stone, marble, etc. Its high-pressure clamping crushing method can effectively handle large pieces of hard materials, so it is often used as a common primary crushing equipment in sand and gravel aggregate production and construction and is widely used in sand making production lines in industries such as mines, sand and gravel plants and metallurgical industries.
- River Pebbles
- Quartz
- Lime Stone
Different degrees of crushing
Hammer crushers are suitable for processing materials with a compressive strength of ≤150 kg/㎝², and their discharge particle size is usually 10-19mm. The jaw crusher has a larger crushing ratio and can evenly crush materials with a compressive strength of ≤350 MPa and the discharge particle size can be adjusted according to demand, ranging from 10-90mm.

The jaw crusher is more suitable for crushing materials with higher hardness, especially ores and large rocks. The crushing particle size of the jaw crusher is larger, usually between 10-350 mm.

The difference between crushing particle size and output
The hammer crusher is usually suitable for crushing applications that require finer-grained materials, and its finished product particle size is generally between 1-25 mm. When processing soft materials, the hammer crusher can provide higher output and is suitable for large-scale production. However, the crushing effect for hard materials is relatively weak.
The jaw crusher has a larger crushing particle size, usually providing material particles between 20-350 mm. Its output is lower than that of the hammer crusher, but the jaw crusher can withstand higher pressure and operate continuously and stably, which is suitable for coarse crushing in mining and heavy industry.
Equipment structure and maintenance
In terms of structure, hammer crushers are usually composed of casing, rotor, hammerhead, screen, and other components. Due to its simple structure and fewer parts, hammer crushers are easy to repair and maintain.
The structure of the jaw crusher is more complicated, including moving jaw, static jaw, transmission device, and other parts. However, it has efficient crushing capacity and sturdy design and has strong stability in long-term operation.
Operation and cost analysis
In terms of operation, the hammer crusher is simple to operate, can achieve more automated operation, and reduces labor costs. At the same time, hammer crusher has low energy consumption and small initial investment.
Due to its high working pressure and strong crushing capacity, the jaw crusher has higher operation and maintenance requirements. The energy consumption of the jaw crusher is relatively large, and its initial investment and maintenance costs are higher than those of the hammer crusher. Due to its strong adaptability and durability, the economic benefits of jaw crusher in long-term operation are more obvious.
Summary of advantages and disadvantages
Hammer Crusher Advantages and Disadvantages
- Advantages: It is suitable for a wide range of materials, especially for the crushing of medium and soft materials. Simple operation and convenient maintenance. Low equipment investment and relatively low energy consumption.
- Disadvantages: It is suitable for crushing materials with lower hardness, and the crushing effect of hard materials is poor. The crushing particle size is large and cannot meet the extremely fine crushing requirements.
Jaw Crusher Advantages and Disadvantages:
- Advantages: It is suitable for materials with higher hardness and has a strong crushing capacity. The crushing effect is stable and the long-term operation is reliable. The equipment is durable and can operate for a long time in harsh environments.
- Disadvantages: The equipment structure is relatively complex and the initial investment is high. The energy consumption is large and the operation and maintenance requirements are high.
Conclusion
When choosing crushing equipment, you first need to understand the nature of the material and production requirements (such as the size and shape requirements of the finished product) to ensure that the most suitable crushing equipment is selected.
The hammer crusher and the jaw crusher each have their unique advantages. The selection of suitable crushing equipment should be judged according to specific production needs. If you are processing medium-soft materials and need higher output and finer particles, you can give priority to the hammer crusher. When the material being processed has a higher hardness and higher requirements are placed on crushing efficiency and equipment stability, jaw crusher is a more ideal choice.
Related Articles
Three Common Types Of Jaw Crusher Machine: Advantages And Disadvantages