Inline sifter is a circular vibratory screener specifically for preliminary screening and granular granular materials. It is usually called flour sifter machine and is often used in the food industry, especially in batches to remove impurities in the flour production line.
- Model: SYM-600/800/1000/1200/1500mm
- Material: Stainless Steel 304/316
- Mesh Size: 2-100 mesh
- Layers: 1-2 layers
- Motor: single or double motor
- Capacity: 1-3 tons/hour
- Customized: Acceptable
Price: $790 – $2900 /Set
Working Principle
The working principle of flow through inline sifters is realized by a vibrating motor, and two sets of unbalanced eccentric blocks are installed at the upper and lower ends of the motor shaft. Due to the setting of the phase angle and the unique cross angle between the two motors, the eccentric block can convert the rotational power of the motor into a composite force in multiple directions including horizontal, vertical, inclined and centrifugal, and overlap and transmit on the screen surface, so as to effectively screen the material. By adjusting the phase angle and weight of the upper and lower parts of the eccentric block, the size of the exciting force can be flexibly controlled, further affecting and optimizing the movement trajectory of the material on the screen surface, ensuring the accuracy and efficiency of the screening effect.
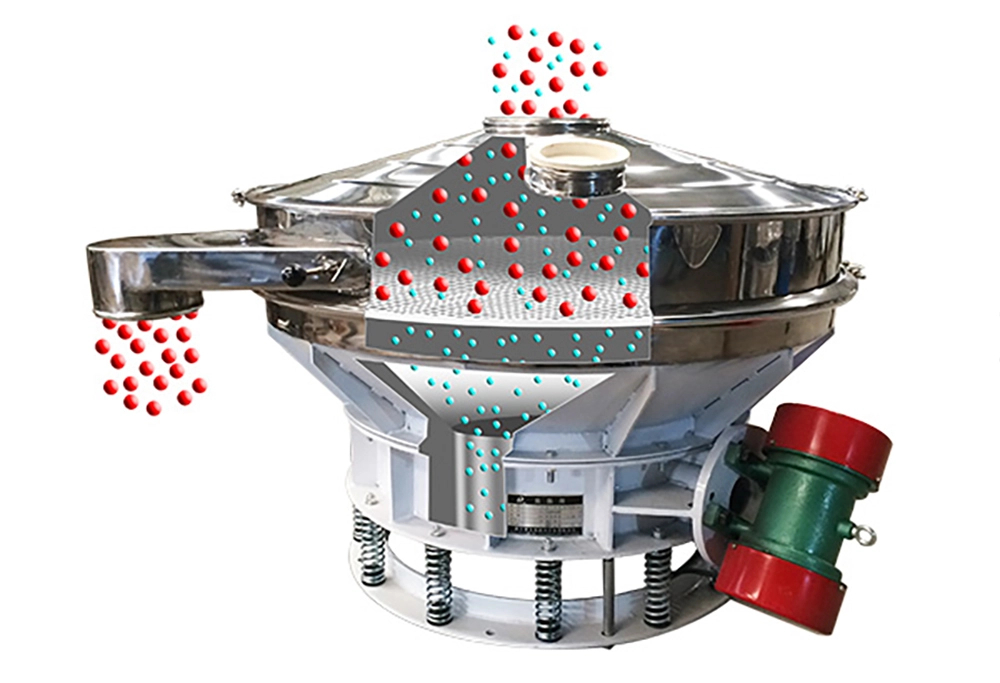
Structures
There are two types of inline vibratory sifters: single vibration source and double vibration source. The single vibration source mainly produces up and down vibration on the material and does not have an automatic discharge function. The double vibration source can produce vortex motion on the screen surface and has an automatic discharge function. It is mainly used for impurity removal and loosening of powder in the process flow of the powder production line.
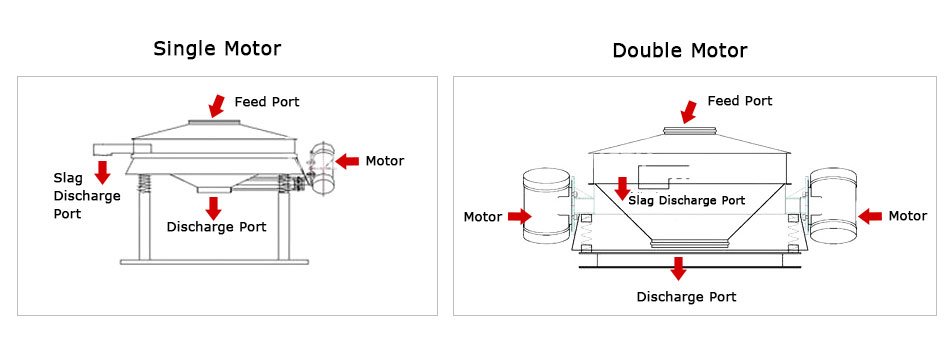
The inline sifter machine is mainly composed of screen, spring, screen frame, tie ring, screen cleaning device and gate. The various components work closely together to achieve efficient and accurate material screening and processing.
- Screen frame: It is usually welded from steel plates, has high strength and rigidity, and is the main part of the inline vibro sifter . The shape and size of the screen frame can be designed and manufactured according to different needs.
- Screen: It is a key component in the inline sifter, used to screen the material according to the particle size. It is usually made of materials such as metal wire and synthetic fiber and has certain strength and wear resistance. During use, the wear of the screen should be checked frequently, and the damaged parts should be replaced in time to ensure the screening effect and equipment life.
- Vibrator (or motor): The power source of the inline sifter, which vibrates the material by exciting the screen frame to achieve the purpose of screening. It is usually composed of a motor, eccentric block, coupling, and other components.
During use, pay attention to the operating status and temperature changes of the vibrator, and perform maintenance and maintenance on time. - Base: The supporting part of the inline sifter, usually made of steel plate. With sufficient stability and load-bearing capacity, the design and manufacture of the base should take into account factors such as the weight of the equipment and the working environment to ensure that the equipment will not shake or deform during use.
- Clamp ring: an important component connecting the screen frame and the screen, used to fix the screen and prevent it from loosening.
Screen cleaning device: used to regularly clean impurities and blockages on the screen to keep the screen unobstructed and the screening efficiency.
Gate: used to control the entry and exit of materials to ensure the smooth progress of the screening process.
According to the specific material characteristics and screening requirements, the inline sifter may also be equipped with dust covers, feed ports, discharge ports, and other components to improve screening efficiency and ease of operation.
Details
- Sieve Frame
- Discharge Port
- Gate
- Control Valve
- Clamp Ring
- Bottom Frame
- Bottom Discharge Port
- Motor
inline sifter Specifications
Model | Power(kW) | RMP(r/min) | Sieve Diameter(mm) |
---|---|---|---|
SYTD-600 | 0.18 | 1460(960) | 520 |
SYTD-800 | 0.25 | 720 | |
SYTD-1000 | 0.37 | 890 | |
SYTD-1200 | 0.55 | 1090 | |
SYTD-1500 | 0.75 | 1390 |
Customized Models of Inline sifter
In addition to standard models, Sanyuantang’s inline vibro sifters can also be customized according to the special needs of specific industries or customers, such as base reinforcement, personalized silo design, base reinforcement, and additional heightening brackets, customized heightening screen frames, motor seat reinforcement solutions, stainless steel elevated screen frames, ordinary models with square or round brackets, and mobile screening systems. We can also further incorporate customized designs such as ultrasonic waves, edge reinforcement, gates, and baffles according to details such as your material properties, production targets, and installation site conditions. To ensure that the equipment configuration we provide accurately fits your needs, please tell us the following key parameters: the name of the material to be screened, the mesh size of the screen, the expected production output, the specific gravity of the material, and the specific location where the installation is planned.
Carbon Steel Stainless Steel Heightened Screen Frame Ordinary Square Legs Heightened Outriggers
Features
Direct discharge outlet design
The outlet is designed at the bottom of the screen, which is conducive to improving the discharge efficiency and is suitable for rough screening processes, such as material impurity removal.
Production line compatibility
It can be directly connected in series with the pipeline system to automatically remove foreign matter and impurities in the pipeline. No manual intervention is required to prevent secondary contamination of materials.
Dust-free screening capability
The equipment has excellent air tightness. Dust does not fly, and it can be used in conjunction with the dust-free feeding station to achieve a negative pressure dust-free working environment.
High space utilization
The motor is external, which reduces the overall height of the equipment and optimizes the use of space.
Durability
The all-stainless steel ring spiral connection is rust-proof, wear-resistant, and prolongs the service life.
Continuous operation capability
The material is automatically discharged, supporting continuous and automated operations to meet 24-hour uninterrupted production needs.
Application
The inline vibratory sifter is widely used in the screening of various powders and granular materials, such as stevioside powder, distiller’s grains, fine powder, powder coating, veterinary drug granules, flour and its impurities (such as insects, stones), Oreo powder, polytetrafluoroethylene particles, fiber cotton, lithium carbonate crystals, lithium fluoride powder, various dye particles, stone powder fine material, ammonium sulfide fertilizer particles, lime fine powder, sand, magnesium oxide particles, plastic additive powder, cement residue, condiment fine powder, polyvinyl alcohol particles, glauber salt crystals, metal powder, chemical basic raw materials, various additives, silicon carbide particles, zinc oxide powder, puffed soybean particles, feed synergistic ingredients, as well as soda ash, sodium metabisulfite, etc. These materials can be roughly classified and precisely screened through the inline screen, showing strong processing capabilities and can be easily integrated into various production line systems.
- Wheat Flour
- Cereal Grains
- Spices
- Oreo powder
- Stevioside Powder
- Medicine Powder
- Lees
- Medicine
- Plastic Additives
- Plastic Particles