What is a Casting Sand Vibrating Sieve?
Casting Sand Vibrating Sieve is a major equipment used in the foundry sand industry for sieving and removing impurities. It is through the way in the vibration, through the sieve mesh and then the casting sand sieving, grading, and removing impurities. The quality of sand used for moulding and core making is even and pure in accordance with the production standard. Commonly used in the new sand into the warehouse pretreatment, old sand / recycled sand reuse screening, sand mixing before screening, casting line after the primary treatment of sand drop, sand regeneration system of the intermediate screening, etc., the common equipment Linear Vibrating Scree, Square Gyratory Screen, Ultrasonic Vibrating Screen, etc.. Let’s take a look at the solution of casting sand vibrating sieve in foundry sand industry.
Casting Sand Vibrating Sieve Common Problems and Solutions in Foundry Sand Industry
In the screening process of foundry sand, vibrating screen is the main equipment, and its stable operation and use of the type of sand quality is very important. However, we often encounter different problems in actual production. Below I list some common problems and corresponding solutions:.
1. Low screening efficiency, insufficient processing capacity:
Problem: Sand is piled up on the screen mesh and cannot pass through quickly, resulting in the output not meeting the requirements.
Causes: screen mesh selection is not right, the vibration parameters (amplitude, frequency) set unreasonable, sand humidity or high mud content leads to bonding, uneven or excessive feeding.
Solution:
- Screen selection: according to the target size of sand particles to accurately select the screen mesh, if necessary, the use of layered screen equipment.
- Adjustment of vibration parameters: according to the characteristics of the sand material to change the amplitude and vibration frequency, to enhance the jumping and transport capacity of the sand material on the screen surface.
- Control of sand: pre-drying or pre-treatment of sand that is too wet or has high mud content, such as adding ash removal and crushing devices.
- Improve the feeding method: use uniform feeder such as rotary valve, vibrating feeder, to avoid centralised impact on the screen mesh, so that the material is uniformly distributed across the width of the screen.
2. Screen clogging (paste mesh):
Problem: Fine powder, wet sand or bonded material clogging the screen holes, preventing qualified sand particles from passing through, affecting the screening effect.
Causes: sand humidity is too high, containing fine powder or sticky substances such as bentonite, too much resin, electrostatic adsorption, screen cleaning device failure.
Solution:
Control the humidity of the material: Control the moisture of the material at source or increase the drying process.
Apply a screen cleaning device:
- Bouncing ball/cleaning ring: Install a rubber bouncing ball or cleaning ring under the screen to vibrate against the bottom of the screen and shake off clogs.
- Air Blowback/Ultrasonic Screen Cleaning: For extremely fine powder or viscous materials, use compressed air blowback system or ultrasonic vibrating screen, high-frequency micro-amplitude vibration or airflow can effectively prevent and remove clogging.
Selection of anti-clogging screen: such as the use of wedge wire screen, self-cleaning screen.
Static electricity elimination: in a particular environment, consider installing static electricity eliminator.
3. Excessive screen wear:
Problem: Short screen life, frequent replacement, increased maintenance costs and downtime.
Causes: Sharp metal particles in sand, especially old/recycled sand, high temperature sand, excessive vibration force, screen material or structure is not wear-resistant.
Solution:
- Pre-treatment: Add iron removers and fine screening equipment before the vibrating screen to remove metal impurities and oversized particles.
- Optimise the vibration parameters: avoid excessive amplitude resulting in excessive impact of sand particles on the screen mesh.
- Choose wear-resistant materials: use high manganese steel, polyurethane (PU), rubber wrapped or composite materials of wear-resistant screen mesh.
- Reduce the temperature of the sand: For hot sand such as after the fall of sand, increase the cooling link or in the design of the equipment to consider heat resistance.
4. Dust pollution:
Problem: The screening process generates dust, polluting the environment and endangering workers’ health.
Causes: the screening process itself produces fine powder, equipment sealing is not strict, dust removal system is inefficient.
Solution:
- Seal the equipment: Improve the sealing structure of the inlet, outlet and all connections of the screen body, such as using rubber sealing strips.
- Equipped with a dust removal system: set up a dust hood above the vibrating screen or key parts, connect the bag duster or cartridge duster, and ensure sufficient suction air volume.
By identifying these problems and implementing appropriate solutions, you can significantly improve the operating efficiency of your Casting Sand Vibrating Sieve. Of course, if you have more vibrating sieve problems, you can also contact us now, we have professional service consultants to answer more vibrating sieve problems for you.
- Perlite
- Oil fracturing sand
- Molybdenum-Powder-Screening-300×246
- Drying sand
- Ceramic sand
- Abrasive
- Plastic Pellet
- Rubber Granules
Casting Sand Vibrating Sieve – Advantages Comparison of Common Vibrating Screens
Below is a comparison of the key advantages of three mainstream equipment types:
Key Advantages | Linear Vibrating Screen | Square Gyratory Screen | Ultrasonic Vibrating Screen |
---|---|---|---|
Throughput | High – Suitable for large-volume, rapid processing (e.g., new sand intake, primary return sand treatment) | Medium-High – Unique trajectory maximizes effective screening area utilization | Medium – Optimized for fine sieving; throughput limited by screen area and ultrasonic power output |
Screening Precision | Good – Up to 100 mesh | Excellent – Extended material residence time ensures thorough separation; precision up to 200+ mesh | Exceptional – Designed for ultra-fine powders; effectively eliminates blinding; precision up to 500+ mesh (e.g., coating sand, fines recovery) |
Anti-Blocking Ability | Moderate – Prone to clogging with wet/sticky materials or fines; relies on cleaning aids | Good – Tumbling motion reduces clogging | Exceptional – Ultrasonic energy generates high-frequency micro-vibrations, virtually eliminating blinding |
Material Adaptability | Broad – Handles dry sand of various sizes (coarse/medium/fine); tolerates moderate moisture | Relatively Broad – Ideal for free-flowing sands requiring high precision; adapts well to slightly sticky sand | Specific – Best for ultra-fines, high-viscosity, agglomerative, or electrostatic materials (e.g., reclaimed sand fines, foundry coating sand) |
Grading Capability | Good – Supports multi-layer screening (typically 2–4 decks) | Excellent – Achieves precise multi-layer grading (often 4+ decks); sharp separations | Good – Primarily for single/double-layer high-precision sieving and impurity removal |
Footprint | Low Height, Long Length | Compact & Square – Moderate height but smaller footprint (square design) | Flexible – Structure similar to standard screens (linear/circular); size depends on deck area |
Energy Consumption | Moderate | Moderate | Higher – Requires additional power for ultrasonic generator |
Maintenance | Relatively Simple – Mature structure, common parts | Moderately Complex – More intricate drive mechanism | Specialized – Ultrasonic transducer system requires expert maintenance |
Typical Foundry Applications | New sand pre-treatment, primary sieving of return/reclaimed sand, pre-mixing screening, primary hot sand treatment after shakeout (high-volume) | High-precision grading (e.g., post-regeneration resin sand grading, coated sand classification), intermediate fine screening in sand systems | Processing ultra-fines in reclaimed sand, removing impurities in coating sand, final precision sieving for high-demand sands (e.g., investment casting) |
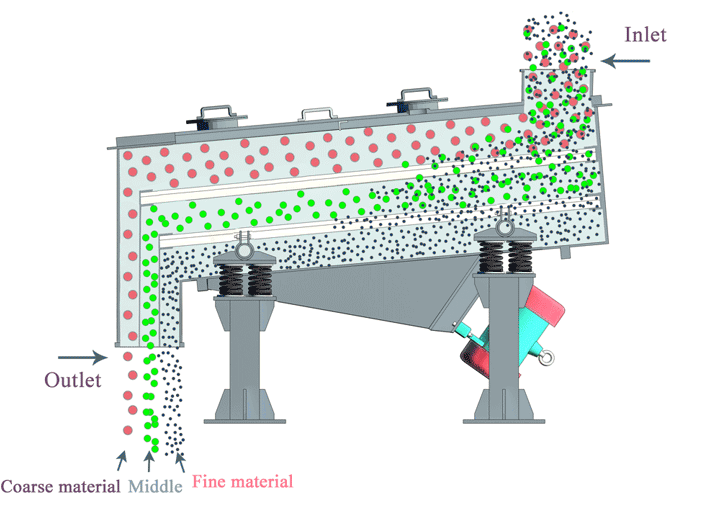
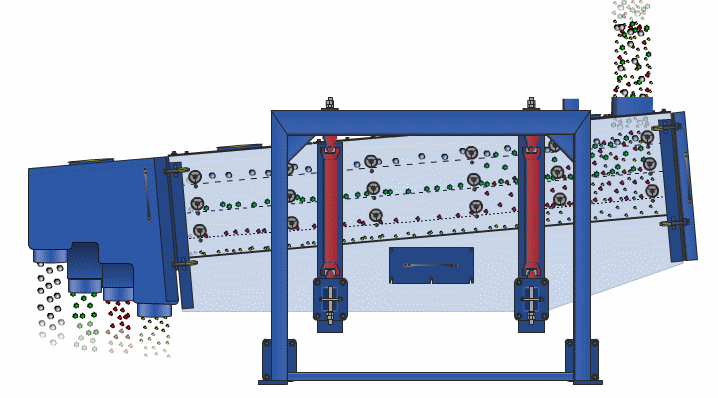
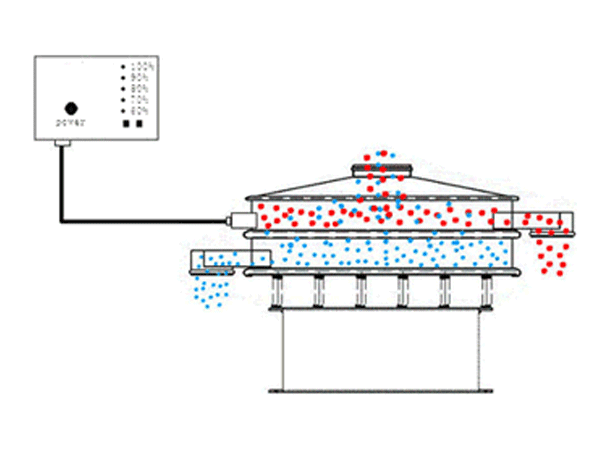
Conclusion:
Through the content of the above article we know that Casting Sand Vibrating Sieve solution in foundry sand industry. If you now have any vibrating sieving problems now you can contact us, we are the vibrating screen industry manufacturers, with 30 years of vibrating screen manufacturing capacity and professional solutions to a variety of vibrating sieving solutions. We have a professional solution team to answer all kinds of vibrating screening problems and how to buy and so on.