In the sand making production line, if the configuration scheme is unreasonable, a large amount of dust is easily generated during the production process, thereby polluting the environment and not meeting environmental protection requirements. So how to prevent dust in sand making production line? Please continue reading this article.
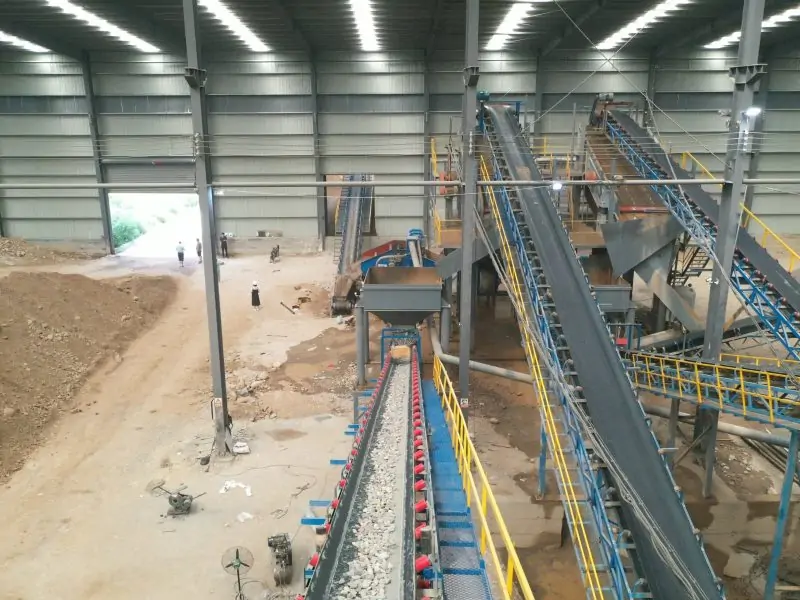
Dust Reduction in Material Field Mining
Optimizing Blasting Parameters and Dust Control Equipment
To meet production needs in the sand making production line, it is crucial to optimize blasting parameters based on specific tests. Besides controlling the raw material particle size, it is necessary to monitor the stone powder content after each blasting process. Key factors like the diameter, spacing, and charge amount of the drill holes should be strictly controlled to minimize dust formation. The use of advanced mobile drills equipped with dust collection systems and protective dust covers at the drill bits can significantly reduce dust during blasting operations.
Reasonable batching and removal of pollutants
By understanding the particle grading of materials processed from different lithologies, raw materials can be mixed strategically for use in the sand making production line. This helps resolve issues such as poor sand grading and fluctuations in fineness modulus. Additionally, fragile, broken, or weathered materials should be removed to prevent secondary dust generation within the system.
Production plan optimization
In the material yard filling process, large height differences in falling materials can lead to an increase in stone powder generation. To alleviate this, the production schedule for the sand making production line should be optimized to minimize the height differences during loading, thereby reducing dust. Maintaining a controllable falling height and consistent material flow can help minimize dust generation.
Atomized water spraying strengthens environmental protection
Investing in environmental protection technologies like atomized water spraying can significantly reduce dust in the sand making production line. This method is especially effective in areas with large drop heights, as it increases the moisture content of the material to reduce dust. Targeted water spraying can be applied at key locations such as sand conveyor belts and vibrating feeders.
Dust control in sand and gravel processing systems
Sand and gravel processing systems in the sand making production line often rely on dry production processes like powder selection machines. With stone powder content exceeding 40% in the sand after crushing, strong vibrations and high drop heights can result in considerable dust generation. Effective dust control measures must be in place to minimize the impact of dust on the working environment.
Implementation of closed systems
To limit the spread of dust during production in the sand making production line, key areas such as crushing workshops and unloading points are fully enclosed. This includes sealing the coarse, medium, and fine crushing workshops and the powder selector discharge port. Additionally, belt chutes and atomizing nozzles are installed at unloading points to further control dust emissions and improve overall system performance.
Humidity control and high-altitude atomization
Dry materials with high stone powder content are prone to dust generation during processing, especially in areas with significant drop heights. To combat this, the sand making production line utilizes both humidification and high-altitude atomization technologies. Water is added at various points, including the feed port of the coarse crushing workshop and the head of the sand conveyor belt, to increase material moisture content. This reduces dust generation in both coarse and fine crushing workshops, ensuring the quality of the finished sand while minimizing dust from falling materials.
Dust removal measures
In a closed system, the main dust-prone areas are the discharge ports of impact crushers in the medium crushing workshop and vertical shaft crushers in the fine crushing workshop. Sealing these locations can hinder equipment observation and maintenance. Additionally, humidifying the materials here may adversely affect the quality of the finished sand (since the powder selector requires dry screening machine). Therefore, bag dust collectors are installed in the fine crushing workshop and the powder selector workshop to effectively capture dust without obstructing equipment inspection and maintenance.
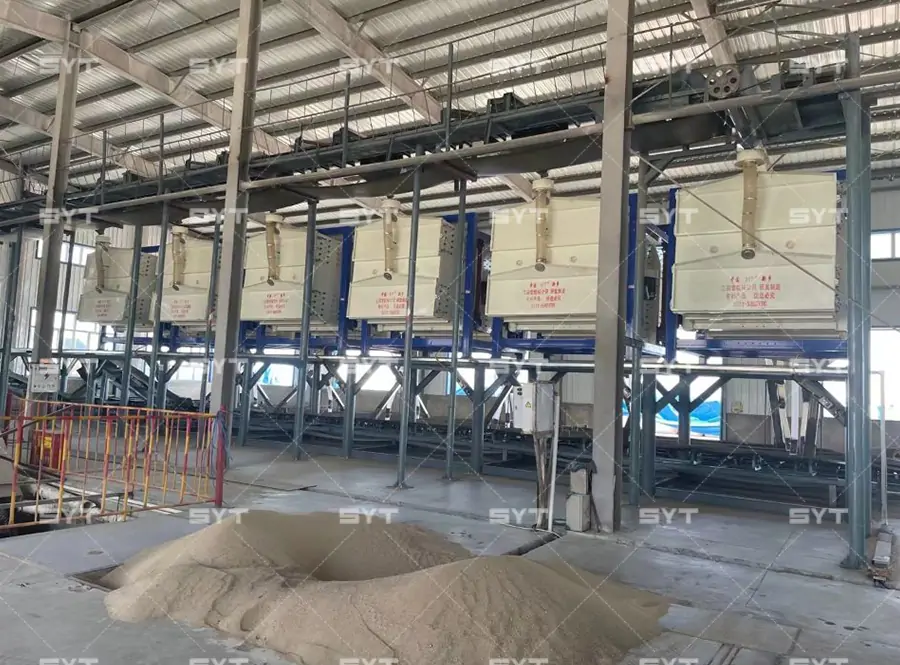
The powder selector outlet in the sand making production line is prone to air leakage, which causes dust pollution. To address this, a star-shaped discharger—commonly used in cement plants—can be installed at the finished sand outlet to reduce air leakage and minimize dust emissions, thereby improving environmental standards.
Dust removal modification of powder selector
The finished sand outlet of the powder selector has a problem of air leakage, resulting in a large amount of dust leakage, which is easy to cause dust pollution. In order to more effectively reduce this pollution and meet environmental protection standards, after investigation, it was found that the star-shaped unloader has better air locking performance in the cement industry. Therefore, a star-shaped discharger can be installed at the finished sand outlet of the powder classifier to reduce air leakage, thereby controlling and alleviating dust pollution problems.
System wastewater treatment Solutions
The sand making production line primarily relies on dry production processes. Water is mainly used for coarse aggregate washing and spray dust suppression. The total water consumption is approximately 100 cubic meters per hour, with 70 cubic meters per hour used for washing and 25 cubic meters per hour for dust suppression. Wastewater treatment is minimal, as the suspended solids content is low. The treatment process uses natural sedimentation in a sedimentation tank, followed by chemical treatment to promote sedimentation, after which the clarified water is recycled.
Conclusion
In a sand and gravel production line, dust control measures are key to maintaining a healthy working environment and ensuring efficient operation of the production system. Dust emissions can be effectively reduced by optimizing blasting parameters, improving material handling methods, implementing comprehensive dust control measures, and investing in advanced environmental protection technologies.