Overview
A calcium powder manufacturer sought a large output gyratory screener to enhance their production process. The primary requirements were high efficiency, high precision, and large output for screening calcium carbonate powder. The solution needed to ensure stability and reliability during the screening process and support multiple screening levels simultaneously.

The gyratory screener has the characteristics of high efficiency, high precision, and large output for screening calcium carbonate powder, and can meet multiple screening levels at the same time. The square swing screen can ensure the stability and reliability of calcium carbonate powder during the screening process and provide strong support for the production of calcium carbonate powder.
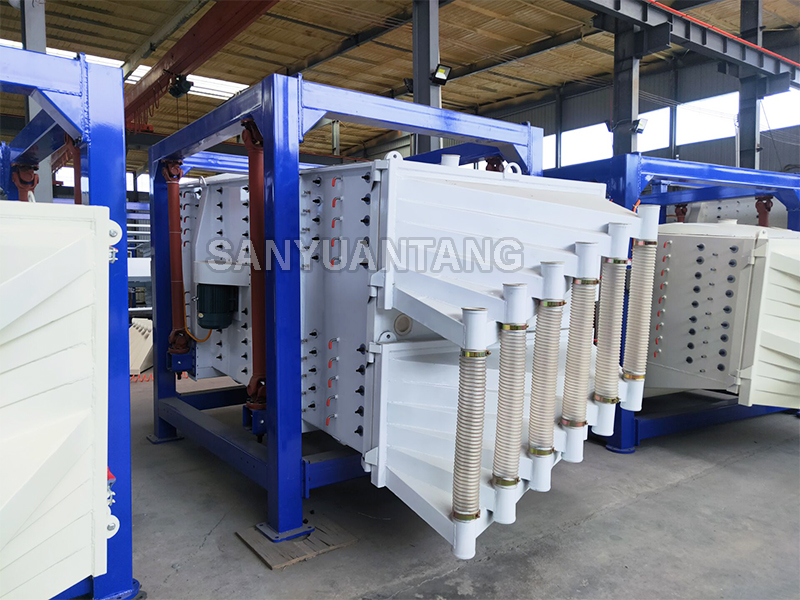
What is Calcium Powder?
Calcium powder (Calcium), commonly known as limestone, or stone powder, the main component is calcium carbonate, is weakly alkaline, insoluble in water, and soluble in acid. It is a common substance on the earth, found in aragonite, calcite, chalk, limestone, marble, travertine, and other rocks. It is also the main component of animal bones and shells.
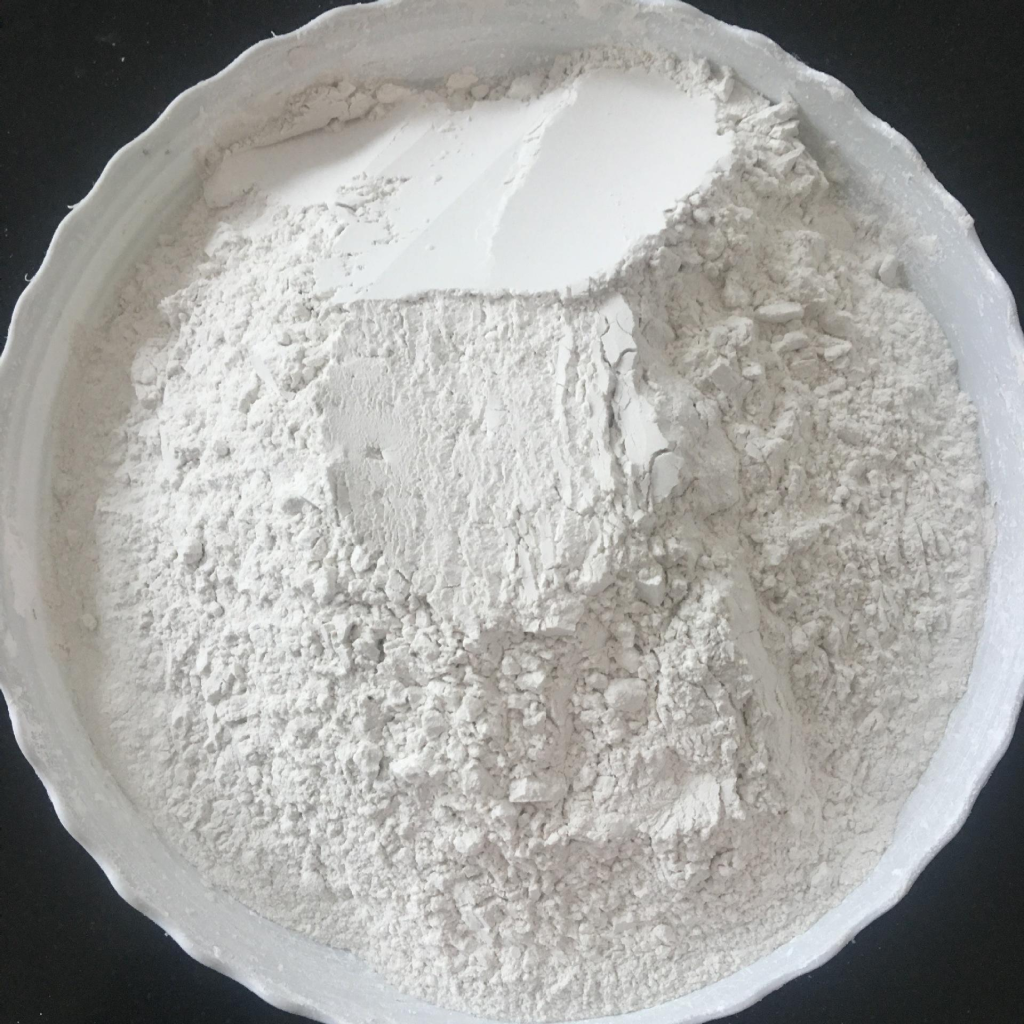
The Production Method of Calcium Powder
1. The raw material of calcium powder is limestone, and in mining, it is necessary to choose a limestone mine with high calcium content and fewer impurities for mining.
2. The extracted limestone is initially broken to remove large particles with greater hardness for later screening work.
3. The crushed limestone material is sifted through a sieve to remove particles that do not meet the requirements. It can be used gyratory sifter, linear vibrating screen, circular tumbler screen, and rotary vibrating screen. The type of screening machine can be selected according to the screening accuracy and yield
Calcium Powder Sifting Solutions
- Actual equipment: Double vibration source gyratory screener
- Screening material: Calcium powder
- Test time: 1.5 t/20min
- Material powder content: 80%
- Test material count: 20 mesh, 40 mesh, 60 mesh, 80 mesh, 120 mesh
Results
After understanding the screening solutions provided, the calcium powder manufacturer visited our factory to see the gyratory screener in action. The trial operation of the gyratory screen machine was successful, leading to immediate customer satisfaction. Consequently, the customer ordered two units of the gyratory screener on the spot, confident in the equipment’s ability to meet their stringent requirements.
The gyratory screener effectively addressed the customer’s needs for high efficiency, precision, and large output in the calcium powder production process. The solution provided reliable and stable screening, supporting multiple levels of classification and ensuring consistent product quality. This successful case highlights the effectiveness of the gyratory screener in optimizing calcium powder production.
Why choose the gyratory screener for calcium powder sifting?
1. Rich Gyratory Screener Sifting Cases
2. Gyratory Screener Advantages
- 1. Reasonable design, mature technology, easy to install, easy to maintain, wide range of applications.
- 2. High screening efficiency, accurate screening precision, and large processing output.
- 3. Screen replacement is more convenient and quick, higher utilization rate, and has a longer service life.
- 4. Self-cleaning screen in the screening process, good effect, noise reduction.
- 5. The whole machine sealing effect is complete, both to reduce energy and ensure environmental protection.
3. Gyratory Screener working principle
The gyratory screener effectively simulates the effective principle of artificial screening movement (screening accuracy, efficiency, and screen life is 5-10 times that of the conventional circular sieve), in line with all fine and ultra-fine ranges of powder and particulate materials, especially suitable for difficult to handle materials.
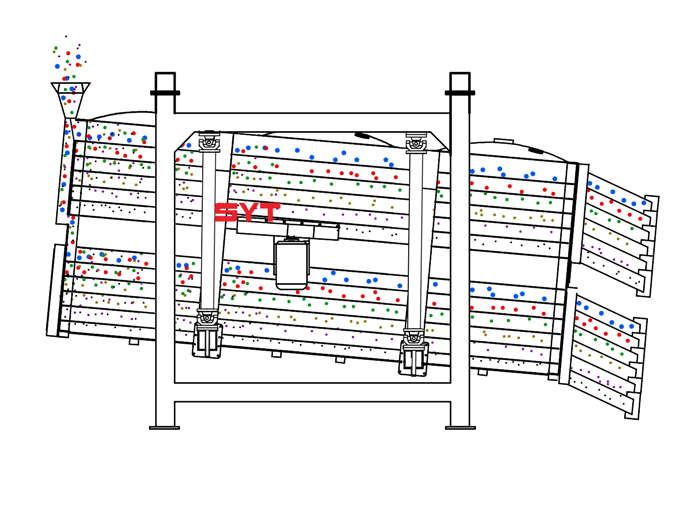
The gyratory screen box in the role of inertial force for back and forth reciprocating motion, and drives the screen surface to do periodic shaking, prompting the material on the screen surface with the screen box to do directional jumping movement, smaller than the screen aperture of the material through the sieve frame to the lower layer, known as the sieve, larger than the screen aperture of the material by the continuous tumbling and jumping movement from the front discharge port, and then complete the screening operation.