The bucket elevator conveyor is a vertical conveyor feeder equipment that adopts a plate chain structure and gravity-induced unloading principle. It can vertically convey various bulk, granular, and block materials, including but not limited to grains, feed, coal, and ore. The lifting height of the bucket elevator can reach 80 meters, the commonly used height is generally less than 40 meters, and the conveying capacity can reach 1,600 cubic meters per hour.
Type: Belt/Chain
Suitable Material Size: 25-70mm
Lifting capacity: 5.4-142 tons/hour
Lifting height: ≤40 meters
Lifting speed: 1.4-2 m/s
Material: carbon steel, stainless steel
Application: It is used to lift and convey foundry sand, silica sand, quartz sand, calcium carbonate, and other materials.
Working principle
The working principle of the bucket elevator conveyor is based on the rotation of the motor-driven reducer and sprocket, which in turn drives the chain and bucket to move continuously. When the bucket moves to the top of the elevator, it is smoothly lifted to the discharge port through the rolling support of the drum, and the material is dumped out of the bucket. Subsequently, during the descent, the bucket tilts due to gravity, allowing the material to naturally flow into the bucket, achieving smooth and continuous transportation.
Structures
Structure: The bucket elevator is mainly composed of running parts, traction parts (conveyor chain), driving device, upper device, middle casing, lower device, feeding port (inlet), and discharging port (outlet).
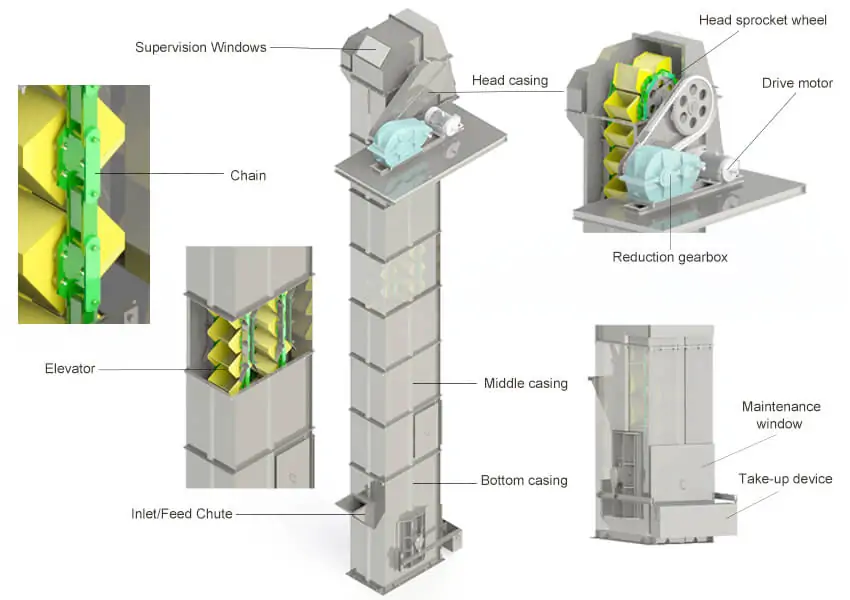
Buckets:
Function: The primary components responsible for carrying materials.
Design: Available in various shapes and sizes, often made of metal or plastic, depending on the application.
Casing (Enclosure):
Function: Encases the elevator, providing structural integrity and protection.
Design: Typically made of steel, it can be square, rectangular, or circular in cross-section.
Belts or Chains:
Function: Provide the mechanism for lifting buckets.
Design: Belts are usually made of rubber or plastic, while chains are made of metal. The choice depends on the type of materials being transported and the operating conditions.
Head Section:
Function: Houses the drive mechanism and supports the bucket’s discharge.
Design: Contains the drive pulley or sprocket, motor, and other drive components.
Boot Section:
Function: Contains the initial loading point where materials are fed into the elevator.
Design: Includes the tail pulley or sprocket and the tensioning device to ensure proper belt or chain tension.
Intermediate Sections:
Function: Provide the vertical structure between the head and boot sections.
Design: Can be of varying lengths to accommodate different lifting heights.
Design Variations:
Centrifugal Discharge Elevators:
Description: Buckets are spaced widely and operate at high speeds. Materials are ejected using centrifugal force.
Applications: Suitable for free-flowing, non-fragile materials like grains and seeds.
Continuous Discharge Elevators:
Description: Buckets are spaced closely and operate at low speeds. Materials are discharged by gravity.
Applications: Ideal for fragile materials or those prone to degradation, like sand or chemicals.
Positive Discharge Elevators:
Description: Buckets are rigidly mounted on two strands of chain, and discharge is assisted by mechanical means.
Applications: Used for sticky or difficult-to-handle materials.
Materials Used:
Buckets: Metal (steel, stainless steel) or plastic (polyethylene, polyurethane).
Casing: Typically steel, can be stainless steel for corrosive environments.
Belts: Rubber or PVC.
Chains: Hardened steel.
Details Show
Specifications
Model | Size of material(mm) | Speed of Bucket (m/s) | Bucket Capacity (L) | Capacity (m3/h) |
---|---|---|---|---|
TD-630 | 50-195 | 0.5 | 2.5-501.8 | 15-800 |
TD-500 | 50-195 | 2.5-501.8 | 15-800 | |
TD-400 | 50-195 | 2.5-501.8 | 15-800 | |
TD-315 | 50-195 | 2.5-501.8 | 15-800 | |
TD-250 | 50-195 | 2.5-501.8 | 15-800 | |
TD-160 | 50-195 | 2.5-501.8 | 15-800 | |
More model can be customized |
Features
- Large conveying capacity, stable and reliable operation, using advanced design principles and processing methods, the trouble-free time can exceed 20,000 hours, the conveying capacity is 10-830m3/h, and the lifting height can reach 50m.
- The whole machine casing is divided into single and double-channel structures. The constant force of the weight box inside the machine can be automatically tensioned. The sprocket is a replaceable wheel rim combined structure, which is easy to replace, long service life,
- Suitable for loose density less than 1.5t/m³, easy to take out powder, granular, small block low abrasive materials. The conveying material temperature does not exceed 250℃: good sealing and less environmental pollution.
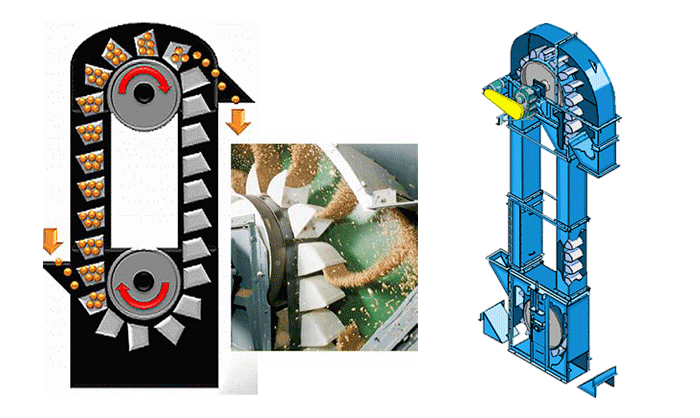
Different types of Bucket Elevator
Bucket elevator can be divided into two kinds of chain elevator and belt elevator according to the traction member. According to different materials can be divided into carbon steel and stainless steel two types. According to different discharging methods, bucket elevator can be divided into: centrifugal discharge, gravity discharge and mixed discharge three forms.
Classification according to the traction member:
- Chain type elevator: strong carrying capacity, high temperatuMaximum conveying capacity 5.4-2m3/h, lifting height 40m.
- Belt type elevator: smooth running, low noise, suitable for light, conventional material transportation. Maximum conveying capacity 5.4-2m3/h, lifting height 50m
- Belt bucket elevator
- Chain bucket elevator
Classification according to manufacturing material:
- Carbon steel bucket elevator: lower cost, high strength. Suitable for general working conditions, no special corrosive requirements of material conveying
- Stainless steel bucket elevator: good corrosion resistance and hygiene performance, easy to clean, more environmentally friendly. Used in food processing industry, chemical industry, pharmaceutical industry and other high temperature or corrosive environment.
- Stainless Steel Bucket Elevator
- Bucket Elevator Conveyor
Classification by discharge method (based on operating speed):
- Centrifugal discharging: using centrifugal force to realize rapid discharging, running speed of about 1.2-4 m/s, suitable for powdery and granular materials with good fluidity.
- Gravitational unloading: rely on the self-weight of the material unloading, running speed of about 0.4-1.0 m / s, suitable for fragile, abrasive materials.
- Mixed unloading: combining the advantages of centrifugal and gravity unloading, running speed of about 0.6-1.6 m/s, suitable for viscous, easy to agglomerate materials.
Application
- Chemicals: resins, coatings, pigments, rubber, carbon black, activated carbon, solvents, glue, sodium sulfate, polyethylene powder, quartz sand, etc.
- Pharmaceuticals: Chinese medicine powder, Western medicine powder, pharmaceutical raw material powder, etc.
- Foods: sugar, salt, monosodium glutamate, starch, milk powder, soy milk, juice, rice flour, dehydrated vegetables, juice, yeast liquid, pineapple juice, fish meal, food additives, etc.
- Kiln industry: glass, ceramics, porcelain mud, grinding materials, refractory bricks, kaolin quicklime, mica, alumina, calcium carbonate (heavy), etc.
- Mining and Metallurgy: foundry sand, silica sand, quartz sand, lead powder, zinc oxide, titanium oxide, diamond powder, aluminum powder, iron powder, various metal powders, etc.
- Manufactured sand
- Sand
- Quarz Sand
- Grains
- Plastic Particles
- Clay
- Steel Grit
- Hardware Accessories
Customize Bucket Elevator
One-stop customize conveying and Screening solutions
Get a Quote
Customer Site
Bucket Elevator Manufacturer
As a leading Bucket Elevator manufacturer in China, Sanyuantang has become an expert in providing total conveying and screening solutions with 30 years of deep cultivation in the industry. Here are our core advantages:
Source Manufacturer, Quality Assurance
With independent production capacity, we implement strict quality control from raw material purchasing to finished product leaving the factory to ensure that each piece of equipment meets international standards.
Affordable and cost-effective
Scale production and lean management effectively reduce production costs and provide customers with cost-effective solutions.
Precision craftsmanship and leading technology
Our R&D team is composed of senior engineers in the industry, following the design concept of “Ease Sieve” to continuously innovate and optimize product design. We use high-precision processing equipment and advanced technology to ensure smooth operation, low noise, low energy consumption, to meet the needs of efficient production.
Support customization, flexible adaptation
For the special needs of different industries (such as cement, chemical, grain, metallurgy, etc.), we provide customized design services, from equipment size, material to functional configuration can be tailored.
Sturdy and practical, durable and reliable
The equipment is made of high-quality steel and wear-resistant materials, with excellent anti-wear and anti-corrosion properties, suitable for a variety of harsh working conditions, and the service life far exceeds the industry average.
After-sales protection, the whole process is worry-free
Perfect after-sales service system provides 24-hour quick response, remote technical support, on-site repair and regular maintenance services. At the same time, we provide customers with comprehensive operation training to ensure the efficient and stable operation of the equipment.