The vibrating sieve machine is also called a vibrating screen separator, vibro-sifter. It is a high-precision fine powder sieving machine with low noise and high efficiency.
Vibrating sieve machines are mainly used in the classification, filtration, and impurity removal of dry powder and wet materials in various industries such as food, pharmaceutical, chemical, and metallurgy.
- Model: SY-600/800/1000/1200/1500/1800 mm
- Material: Stainless Steel 304/316/Carbon Steel
- Mesh Size: 5-500 mesh
- Layers: 1-5 layers
- Motor Power: 0.25-3 kw
- Capacity: 100Kg – 3 Tons/hour
- Service: 5 days delivery/30 days return/support customization/one-year warranty/lifetime service
Price: $799 – $2599 /Set
- Wheat Flour
- Milk Powder
- Oil Fracturing Proppant
- Grain Pellets
- Medicine Powder
- PP/PE Granules
- Paint Coating
- Metal Powder
- Emery
Application
- Industry: Resin, paint coating, cosmetics, paint, Chinese medicine powder, etc.
- Food industry: Powdered sugar, starch, flour, salt, rice flour, milk powder, soy milk, egg powder, soy sauce, fruit juice, etc.
- Metal, metallurgy mining industry: Aluminum powder, lead powder, copper powder, ore, alloy powder, welding rod powder, manganese dioxide, electrolytic copper powder, electro-magnetic material, grinding powder, refractory material, kaolin, lime, alumina, heavy calcium carbonate, quartz sand, etc.
- Others: Waste oil, waste water, dyeing and finishing wastewater, auxiliary agents, activated carbon, etc.
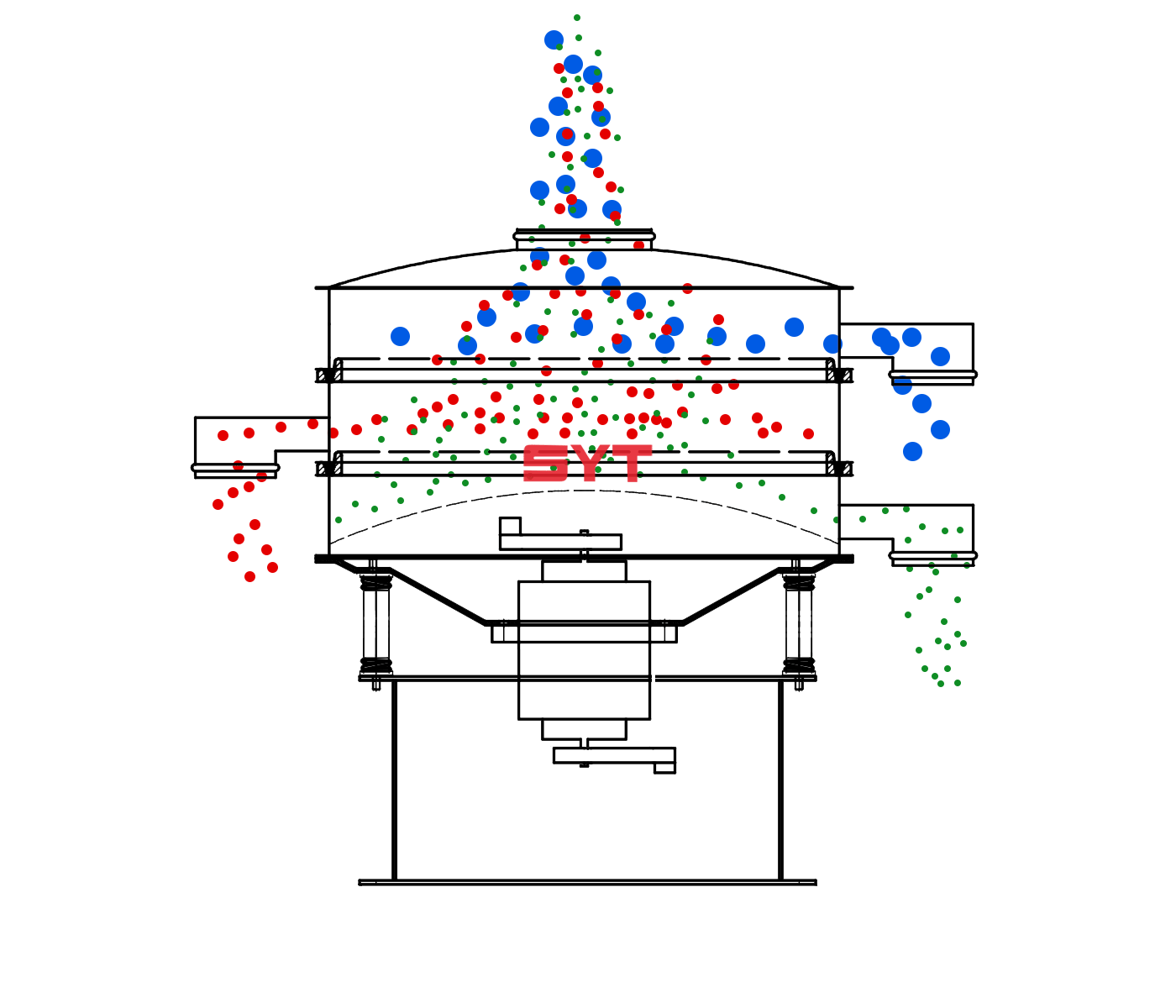
vibrating sieve machine Working Principle
The principle of the gyro vibratory sieving machine is to use the heavy hammer installed above and below the motor shaft (unbalanced hammer) to transform the rotary motion of the motor into horizontal, vertical, and inclined three-dimensional motion, and then transfer this motion to the screen surface, so that the material does the outwardly expanding involute motion on the screen surface.
The rotary vibrating sieve machine has the advantages of long trajectory of material running and a high utilization rate of the screen surface. By adjusting the phase angle of the upper and lower hammers, the trajectory of the material on the screen surface can be changed. It can be used for fine screening and probability screening of materials.
Main components:
The overall structure flow chart of the circular vibrating sieve: feed inlet, upper cover, small bunch ring, upper frame, discharge port, sub-network, grid, rubber ball, isolation ring, ball tray, rubber skin, bunch ring, middle Frame, lower cone body, bottom frame, outlet, rubber skin, large beam ring, large plate, vibrator tube, motor, upper spring seat, spring, lower spring seat, bottom tube, access door, floor mats.
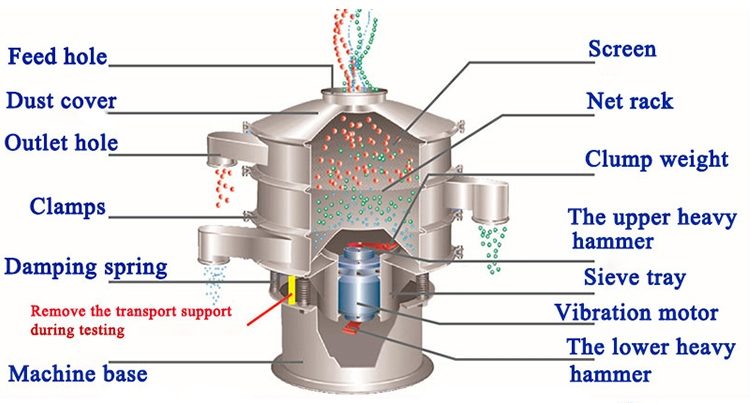
Details Show
- Dust cover with inlet
- Outlet
- Clamps
- Sieves
- Gate
- Damping springs
- Drive base with motor
- Motor
Specifications
Model | Layer (s) | Granularity (mm) | Sieve Mesh | Effective Diameter (mm) | Power (KW) | Capacity(Kg/h) |
---|---|---|---|---|---|---|
SY-XZS400 | 1-3 | <20 | 2-500 mesh | 380 | 0.25 | 100 |
SY-XZS600 | 1-3 | <20 | 3-500 mesh | 580 | 0.55 | 200 |
SY-XZS800 | 1-5 | <30 | 3-500 mesh | 780 | 0.75 | 500 |
SY-XZS1000 | 1-5 | <30 | 3-500 mesh | 970 | 1.1 | 800 |
SY-XZS1200 | 1-5 | <30 | 3-500 mesh | 1170 | 1.5 | 1200 |
SY-XZS1500 | 1-5 | <50 | 3-500 mesh | 1470 | 2.2 | 1500 |
SY-XZS1800 | 1-5 | <50 | 3-500 mesh | 1770 | 3.0 | 2000 |
Custom according to Your Needs
Vibrating sieve machines are available in 3 materials: stainless steel, carbon steel, and plastic to meet the screening needs of different industries.
The standard vibrating screen machine body and material contact part are made of selected 304 stainless steel, and the machine base part is made of carbon steel. The whole machine can also be made of stainless steel according to user requirements (stainless steel vibrating screen), as well as a plastic vibrating screen designed for special chemical materials. In addition, according to the screening grade of the material, you can choose to customize a single or multi-layer screen, as well as add an ultrasonic device.
Contact Part Stainless Steel + Carbon Steel Full Stainless Steel Carbon Steel Anti Corrosion Plastic PP
Vibrating sieve machines with allowable production capacity from 100 to 3300kg/h are widely used for screening and filtering of granular, powdery, and viscous materials, including food, feed, plastic particles, ceramic powders, metal powders, etc. It can be fully customized according to your application requirements. Such as gate type, add edge type vibrating screen, and so on.
Add hopper Add scraper Extended feed port Open type
Features
- Closed structure, less slurry spillage, meeting environmental protection requirements.
- The outlet direction can be adjusted 360 degrees, and impurities and thick and fine materials are automatically discharged from different material ports.
- The new design of the primary and secondary screen structure allows quick screen installation and screen change in 3-5 minutes, reducing
- Optional automatic cleaning systems (bouncing ball/ultrasonic) make the mesh less likely to be blocked and improve screening efficiency.
- It can be used in a single layer or multiple layers, and the materials are divided into 2-6 levels at the same time.